Introduction
CNC Metal Cutting (Computer Numerical Control) machines whir with activity, turning raw metal inventory into everything from aerospace parts to medical implants with remarkable precision. It’s similar to having a superhuman sculptor – one that never gets fatigued, never gets it wrong, and works with precision measured in thousandths of an inch.
What is CNC Metal Cutting?
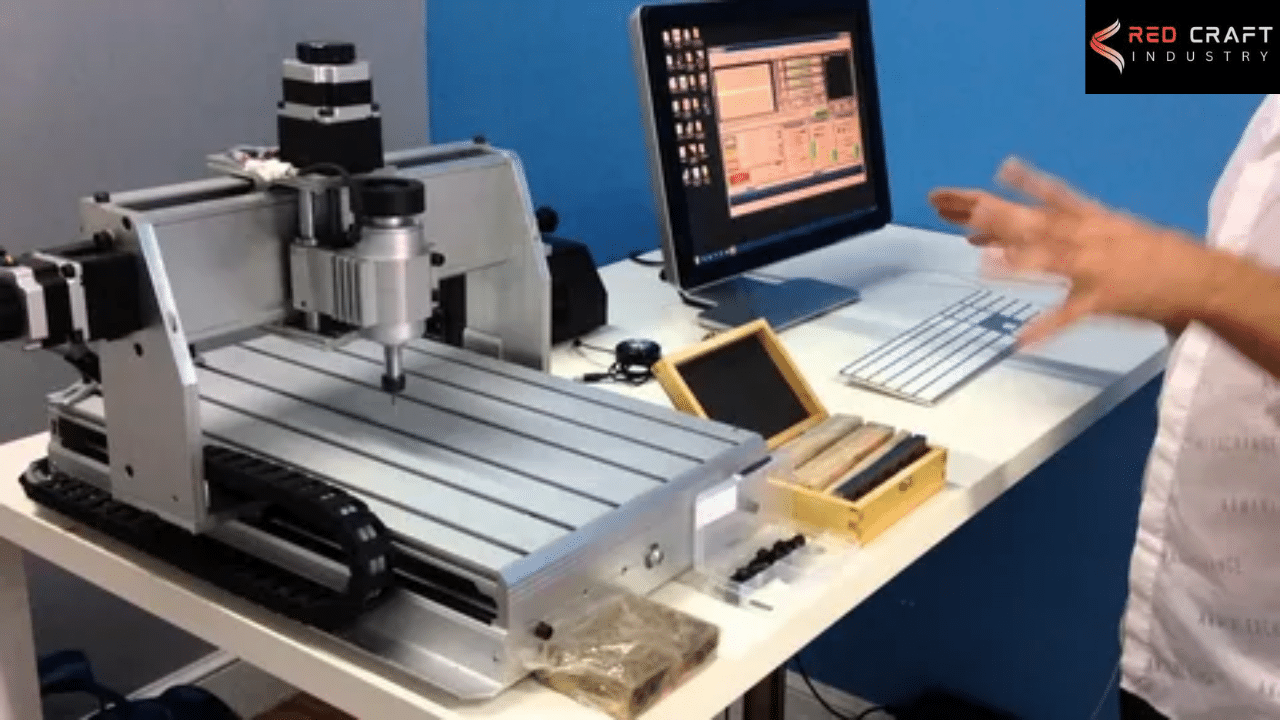
CNC metal cutting is equivalent to having a master craftsman whose hands do not tremble and whose eyes do not skip a single detail – except instead of hands, we have precision-cutting tools whose movements are controlled by advanced computer controls. CNC Metal Cutting denotes Computer Numerical Control, which says it all about how this technology operates: computers convert digital designs into precise numerical commands that drive the cutting tools’ motion.
As opposed to conventional machining in which human machinists physically manipulate cutting movements, CNC technology does the job automatically. You begin with a digital model usually designed through Computer-Aided Design (CAD) software which is translated into machine language. This information instructs the CNC Metal Cutting precisely how to direct its cutting tools in order to cut up raw metal into your intended component.
The sorcery lies in where these computer instructions intersect with the real world. CNC Metal Cutting machines can produce tolerances as low as ±0.0001 inches (roughly 1/4 the thickness of a human hair!) and repeat the same outcomes hundreds or thousands of times. This union of precision, repeatability, and automation has transformed manufacturing throughout nearly every industry.
Evolution of CNC Technology in Metal Fabrication
The actual revolution started in the 1970s and 1980s when microprocessors made actual computer control possible, substituting cumbersome tape systems with digital memory and processing. Suddenly, machines could hold several programs and execute ever more complicated operations. The advent of CAD/CAM (Computer-Aided Design/Computer-Aided Manufacturing) systems further pushed this development, establishing a digital pipeline from design to production.
Key Components of CNC Metal Cutting Systems
The CNC Control Unit
Consider the control unit to be the brain of the whole operation. the place where digital designs take form. It is where programmed instructions are translated and interpreted, becoming exact electrical signals that guide the machine’s movements. Intuitive touchscreen interfaces are what come with latest CNC Metal Cutting controllers, which would make smartphone users feel perfectly at home.
Within the controller, dedicated processors perform real-time computations needed for precise, smooth motion of the tools. They provide for considerations such as acceleration, deceleration, and the intricate mathematics of tool paths. Several contemporary systems even have adaptive controls that are able to change cutting parameters on the fly according to sensor feedback tracking the cutting operation.
Machine Beds and Frames
The bed and frame are the structural base that make precision cutting possible. Usually made from cast iron, welded steel, polymer concrete, or composite material, these parts must withstand vibration, stay aligned under heavy weight, and offer dimensional stability in changing temperatures.
Machine builders utilize numerous approaches to improve stiffness, such as strategic ribbing, optimal distribution of material, and deliberate sensitivity to points of stress. High-precision equipment even has active vibration damping technology built into the equipment or uses dedicated vibration-insulated foundations in order to move around in space.
Cutting Tools and Tool Changers
CNC machines utilize specialized cutting tools for specific operations. These specialized tools are made to keep sharp cutting edges while tolerating the brutal heat and pressure of metal cutting.
Advanced CNC equipment has automatic tool changers that can switch between dozens or even scores of tools without human intervention. Picture yourself cooking in a kitchen where the ideal knife for every job simply appears in your hand at just the right time – that’s basically what these systems offer to machining processes.
Tool management is now an art form in itself, with sophisticated systems monitoring tool usage, forecasting wear, and scheduling maintenance to avoid quality problems or unscheduled downtime. Some state-of-the-art systems even employ vision systems to automatically inspect tools between uses, providing maximum performance during the production cycle.
Popular CNC Metal Cutting Processes
CNC Milling for Metal Applications
CNC milling is the opposite of sculpting – instead of applying material to build a form, rotating cutting tools remove metal precisely where it does not need to be. The process is superb at creating small geometries, flat faces, contours, slots, and pockets in a wide range of metals.
In milling operations, the workpiece is typically held still with multi-point cutting tools whirring at rapid speeds around it, coming into contact with the material in a bid to shave off tiny chips. Movement is dictated by the CNC controller along a series of axes so that the cutting tool will travel toward the workpiece at different angles and cut out intricate three-dimensional shapes.
The flexibility of milling makes it crucial to many different industries. It is just as comfortable making aerospace parts with intricately shaped weight-saving pockets as it is making precision molds for consumer goods. From the creation of proof-of-concept through the production in high volumes, milling is among the most universally used CNC metal cutting methods.
Vertical vs. Horizontal Milling Considerations
In choosing a milling method, orientation is very important. Vertical milling centers (VMCs) have the spindle in a perpendicular position to the work surface – like boring directly down into a board of wood. This type is best suited for detailing work, engraving, and operations that need to see a direct line.
Horizontal milling centers (HMCs) have the spindle aligned parallel to the work surface, cutting materials from the side as opposed to above. This orientation provides superior chip evacuation (think how much easier it is for sawdust to fall away when cutting horizontally versus downward), which makes it well-suited for heavy material removal and larger workpieces.
CNC Turning and Lathe Operations
Whereas milling shines at producing complicated geometries with flat surfaces and pockets, turning operations meet the needs of a completely different group of manufacturing requirements. In turning, the workpiece is spun against fixed cutting tools – ideal for producing cylindrical parts with external and internal details.
Picture holding a potato and turning it against a peeler – that’s the concept behind how turning works, just with infinitely better precision and ability. The CNC lathe turns the work at regulated speeds and moves cutting tools along multiple axes to produce precise diameters, tapers, threads, and contours.
CNC Plasma Cutting Solutions
Plasma cutting really excels at cutting sheet metal and plate material from a few inches thick. Plasma cutting is widely applied in fabrication shops, shipbuilding, automotive production, and construction to fabricate custom parts from generic stock materials. Not having the high tolerance capability of milling or turning, plasma cutting is still an unbeatable blend of speed, flexibility, and economical effectiveness for most applications.
CNC Machine for Metal Cutting
Assessing Machine Specifications
Buying a CNC machine without knowing key specifications is equivalent to buying a car without an idea of what the horsepower or fuel economy figures represent – you may get lucky, but more likely you will end up with something that will not do the job. Systematic review of machine specifications will guarantee you are investing in the appropriate capability.
Work envelope sizes inform you of the largest size of material you can handle – but don’t forget that tool clearances and fixtures cut into this working area. Axis travel requirements specify how far the machine can travel in each direction, and rapid traverse rates specify how fast it can move between cutting operations.
Production Volume Considerations
The ideal CNC solution for a one-off and small batch custom shop may be entirely inappropriate for high-volume production facilities. Volume needs have a dramatic effect on machine selection, with varying optimization priorities depending on the production situation.
Low-volume production frequently makes use of versatile, multi-purpose machines that can rapidly be set up for a wide range of part types. Minimizing setup time features is important in such conditions since machines can be reset numerous times per day for other parts.
High-volume manufacturing generally calls for more specialized machines optimized for particular operations. Pallet changers, robotic loading/unloading, and in-process inspection features reduce non-cutting time and provide consistent quality for large production runs. The initial capital investment might be greater, but the per-part cost savings pay off rapidly at volume.
Behind each CNC action is a dedicated language that computers can comprehend: G-code. Consider it to be the alphabet and syntax through which humans are able to communicate cutting commands to machines. Although it may appear daunting at first glance – riddled with letter addresses, coordinate values, and specialized commands – the basics are really very accessible.
CAM Software Solutions
Today’s CAM systems have large knowledge bases regarding cutting tools, materials, and machining methods. They are able to select suitable cutting parameters automatically, optimize tool paths for efficiency, and simulate operations to detect potential issues before actual cutting takes place. It’s similar to having the knowledge of an experienced machinist in software form.
The CAM landscape extends from basic 2.5D packages appropriate for simple parts to advanced systems that can accommodate intricate 5-axis machining. The ability to integrate with design software, machine-specific post-processors, and simulation accuracy is the major differentiator while considering these essential tools.
Materials Typically Processed with CNC Metal Cutting
The applicability of CNC technology covers almost the entire gamut of metals, although every material has some specific machining attributes and difficulties. Familiarity with these properties of materials considerably influences cutting methodologies, tool choices, and outcomes to be expected.
Aluminum alloys are among the most frequently machined metals based on their superior machinability, light weight, and broad range of applications. They permit high speeds of cutting and can obtain very good surface finishes but, due to softness, often pose problems regarding chip evacuation in deep pocket milling.
Cost Factors in CNC Metal Fabrication
Understanding the true costs of CNC metal cutting goes far beyond the hourly machine rate. It’s a complex equation involving numerous variables – many of which aren’t immediately obvious but significantly impact overall economics.
Direct costs cover machine usage (hourly rates, energy, and actual machining time), tooling cost (including initial tool investment and ongoing replacement cost as tools wear), material costs (both raw stock and the cost of material removed during machining), and labor for setup, operation, and inspection.
Process improvement has great potential for cost reduction. Techniques such as optimized tool paths, effective cutting parameters, effective fixturing, and reduced setup time can significantly decrease per-part cost despite unaltered hourly rates. This is why skilled CNC operators and programmers frequently justify premium pay – their work directly influences the bottom line.
Optimizing CNC Metal Cutting Operations
Tool Path Strategies for Efficiency
The way cutting tools move through material dramatically impacts machining efficiency, tool life, and part quality. Modern CAM systems offer numerous specialized tool path strategies optimized for different operations and objectives.
Safety Protocols for CNC Metal Cutting
Power, velocity, and high-speed cutting tools join to render CNC machines dangerous if not adequately protected by safety measures. Extensive safety practices shield operators, maintenance workers, and bystanders against numerous hazards inherent in metal cutting processes.
Physical guards, such as interlocked enclosures, keep moving components out of reach during operation but contain chips and cooling liquids. Emergency stop systems disconnect power instantly when initiated, whereas safety interlocks inhibit operation when guards are open or safety systems are breached.
New Trends in CNC Metal Fabrication
Multi-Axis Machining Developments
Conventional 3-axis machining (movement in X, Y, and Z coordinates) has been replaced by more advanced multi-axis capabilities. Five-axis machines – adding rotary axes to the conventional three – can move toward workpieces from nearly any angle, allowing single-setup processing of intricate geometries.
These next-generation systems obviate the need for multiple setup, saving handling time, enhancing precision, and allowing geometries not possible with traditional methods. Although initially limited to aerospace and medical industries, declining costs have brought five-axis machining within reach of broader manufacturing sectors.
FAQs
1. What is normal tolerability with high-tech CNC metal cutting machines in normal conditions?
High-technology precision CNC equipment commonly maintains a tolerance of ±0.0005 inches (about 0.01mm) under optimal operating conditions. Ultra-precision equipment can hold even tighter tolerance of about ±0.00005 inches (0.001mm) for specialized use. Real tolerance under practical use is influenced by several factors such as machine quality, maintenance level, ambient conditions, operator expertise, and specific machining operation being used.
2. How do I know whether CNC turning or CNC milling is ideal for my metal part?
The shape of your part is the main consideration. Parts with mostly cylindrical features and rotational symmetry (such as shafts, bushings, and threaded items) tend to be best machined with turning operations. Parts with mostly prismatic features, complex pockets, or irregular shapes tend to be best machined with milling. Most components are actually improved by both processes, and that is why the “mill-turn” shops of today that can do both services are in great demand for complex components.
3. What has the greatest influence on cutting tool life in CNC metal work?
Cutting velocity (contact velocity of the tool edge on the material) has the most severe effect on tool life, and at too high a velocity, greater wear occurs due to heat generation. Feed rate, depth of cut, material properties, tool coatings, cutting fluid use, and machine tool stability are other essential parameters. New “high-efficiency machining” processes with stable cutting tool forces are able to increase tool life dramatically even at higher material removal rates.
4. Are CNC metal cutting processes able to machine hardened steels and other hard materials?
Yes! Hardened materials are hard, but new cutting tools with special substrates and coatings can machine very hard materials efficiently. Ceramic, cubic boron nitride (CBN), and polycrystalline diamond (PCD) tool materials facilitate machining of hardened steels, heat-resistant superalloys, and other challenging materials. Such processes often demand modified cutting parameters, strict heat control, and highly rigid and vibration-controlled machines.
5.How long is the learning curve for an inexperienced CNC programmer and operator?
Basic principles of operating a CNC can be learned in weeks, but to reach actual proficiency, months of practice under supervision are needed. Learning curve is significantly influenced by prior experience (conventional machining knowledge is a source of rich context), part complexity being manufactured, and equipment and software sophistication to which access is available. The best CNC machinists all call their own improvement a continuous process, not a product – even decades after experience, there is always some new thing to learn about technique, technology, and method of optimization.
Year | Milestone | Details |
---|---|---|
1940s | Early Development of NC Machines | Numerical control (NC) was introduced for machining processes using punched tape. |
1952 | First CNC Prototype | MIT developed the first computer-controlled milling machine. |
1960s | Commercial CNC Machines | CNC machines became available for industrial use in metal cutting. |
1970s | Integration with CAD/CAM | Computer-Aided Design (CAD) and Computer-Aided Manufacturing (CAM) systems were integrated. |
1980s | Microprocessors in CNC | CNC controllers became more powerful and compact with microprocessors. |
1990s | PC-Based CNC Machines | More affordable and customizable CNC machines entered the market. |
2000s | Multi-Axis CNC & Laser Cutting Advances | 5-axis and laser cutting CNC machines became widely adopted in metalworking. |
2010s | IoT & Smart CNC Systems | Machines started connecting to the cloud and analytics platforms. |
2020s | AI Integration & Precision Automation | AI, automation, and smart sensors began optimizing cutting precision and efficiency. |
Conclusion
One of the most revolutionary manufacturing technologies – the union of digital design and hard reality that makes modern products possible – is CNC metal cutting. From the phone in your pocket to the automobile you drive, millions of metal parts live on because of these great machines.
As we’ve discovered, successful application of CNC depends on comprehension of many interrelated variables: machine capability, cutting process, tool consideration, programming method, and optimizing techniques. As a production expert, product engineer, or simply someone interested in how things get made, learning these basics gives you good perspective into contemporary manufacturing.
Read more about our services at Red Craft Metal Industry